TRSE Barcode
Transfer |
|
|
|
|
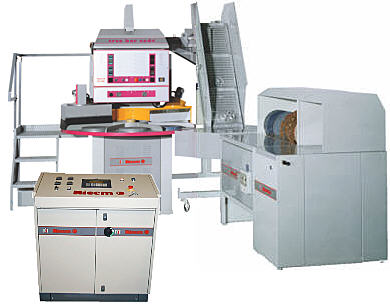 |
After 12 years of study, a number of prototypes and three years of testing the final model, NICEM's department of research and development has now put the finishing touches to the new TRSE BAR CODE casting unit, which represents a synthesis of innovation, reliability and operating pratice.
The high levels of technology adopted and the introduction of the bar code system make the new casting unit a point of reference for applications in this field, assuring improvements in production quality, optimization of production times and, last but not least, continuos monitoring of the state of manufacture of each individual item. |
|
|
The impact of this radically new system on production is comparable to the change brought about by the "CNC" (Computerized Numeric Control) advanced automation. |
|
|
|
|
|
THE BASIC IDEA |
|
|
Previously, all the casting parameters, i.e. centrifuging time, metal quantity centrifuging speed and mould closing pressure,were set up manually by the machine operator. |
|
|
This individual frequently had to re-set these parameters for short production runs in between other work as well as perform, other routine tasks such as loading and unloading moulds, treating moulds with talc, "topping up" the crucible and removing the "risers". |
|
|
In consequence, errors were commonplace, and quality and production levels suffered. |
|
|
However, the new TRSE BAR CODE casting unit now means that these tasks may be perfomed automatically, thus relieving the operator of these functions. The system of bar coding the moulds enables the machine to recognise and set up the four casting parameters automatically |
|
|
HOW THE BAR CODE SYSTEM WORKS |
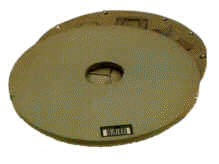 |
|
Each mould has permanently affixed to it a label, capable of withstanding high temperatures, which uniquely identifies it by means of a numerical bar code. A multibar casting scanner, located immediately before the cooling system, reads this bar code wherever it is placed on the mould. |
|
The code read is transferred to a PLC unit installed on the machine which associates it with the corresponding values relating to the mould centrifuging time, metal quantity, mould centrifuging, speed and mould pressure, whose optimal values have been previously stored. |
|
|
The PLC unit in question is capable of handling autonomously a data bank holding 40,000/80,000 items, wich corresponds to 10,000/20,000 moulds. With the aid of an external PC, the storage capacity of the data bank can be infinitely expanded. |
|
|
The PLC unit transfers the resulting data, listed below, to the relevant peripheral units: |
|
|
- centrifuging time
- metal quantity
- centrifuging speed
- mould closing pressure
|
|
|
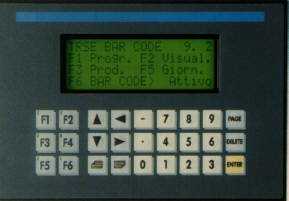 |
The high-speed operating and high precision of the peripheral units enable the settings to be changed instantaneously at any moment during the cycle. |
Where necessary, the BAR CODE operating mode can be shut off using the keypad, which is to be found on the control panel, thus reverting to the traditional operating mode |
|
|
THE PLC UNIT |
|
|
The PLC unit consists of a PLC board, to be found inside the control panel, and of a terminal complete with display and keyboard positioned in the centre of the control panel. |
|
|
All the programming and management functions governing the machine’s adjustment parameters are carried out simply and immedately by means of the keypad and the bcklit display, which provides clear and easy read-out under any conditions. |
|
|
The PLC unit also works as a selfdiagnostic unit, capable of reporting messages relating to operating anomalies or maintenance requirements and functions, a number of which will appear on the display: |
|
|
- pneumatic circuit pressure loss
- pneumatic circuit lubrificating oil low
- warning: safety devices triggered (furnace, table, etc.)
- electrical fault (24 V auxiliary circuit, inverter, duct or furnace elements, table, etc.)
- scanner operating correctly
- daily automatic impurity-purging of air filter
- electronic control of automatic air pressure adjustment
- electronic motor rpm control
|
|
|
* Optional extra: safety check for prevention of double casting |
|
|
THE SYSTEM'S POTENTIALS |
|
|
Apart from the regular management of the production cycle of the new TRSE BAR CODE processing unit, the PLC unit enables the operator to perform operations and applications associated with the organizational management of the work, such as : |
|
|
- programming the week’s furnace swiitch-on and switch-off times
- The possibility of linking two or more TRSE BAR CODEs so as to program the casting parameters on a single machine and store them automatically on other
- production programming and control of every mould and avery machine
- programming/reporting the nummber of castings reached
- the possibility of connecting up to an independent PC
|
|
|
PRODUCTIVITY |
|
|
A patented automatic conveyor feeder completes the new TRSE BAR CODE processing unit, and is capable of feeding risers and ingots gradually into the crucible thanks to a system of level probes fitted in the crucible itself. |
|
|
This means production can be carried out at lower, pratically constant temperatures, and a riser-ingot mixture is maintained throughout the day, thus ensurring the casting parameters are always correct. |
|
|
As a result, the deterioration of the moulds is reduced and, more importantly, the quality of the pieces is improved. |
|
|
Constantly high standards of product quality, the reduction of the number of rejects, the optimization of casting cycle times, and the elimination of periods of unproductiveness owing to the operator’s intervetion are just some of the advantages offered by the advantages offered by the TRSE BAR CODE system. |
|
|
OTHER DETAILS |
|
|
TRSE Barcode Processing Unit
Particulars
Examples of finished products |
|
|
|
|
back |
|
back to top |
|